多种材料正在争夺统治海洋。亚博网站下载钢,铝和复合材料竞争是选择的材料,每次浪潮都取决于所考虑的工艺亚博网站下载。两个世纪前,事情要简单得多,船只和船都是用木头制成的。但是如今,船舶是由钢制成的,小型游艇通常由玻璃纤维增强塑料(GRP)制成,并且由于多种原因,小型商用容器由各种材料制成。亚博网站下载“小型商业船只”涵盖了从快速渡轮,巡逻艇到飞行员船和工作艇的所有内容。这些船只是海洋材料的主要战场。亚博网站下载 Economies of ScaleThe material that is considered first for building small, slow commercial vessels is still steel because it is the cheapest. However, GRPs become competitive if a shipbuilder knows that it is making more than ten identical craft or hulls. The cost of producing a plug and mould can be spread over a number of hulls, and so many small commercial vessels that are built using the same hull design, such as pilot boats, are made from GRPs. Orders for ten or more craft are much less likely as the size of the craft increases, which is why there are few GRP craft more than 20m in size. Materials Selection有两个主要驱动因素用于使用钢材以外的其他材料,速度的渴望以及客户的偏好或偏亚博网站下载见。所有船只的最大“位移速度”与其长度有关。以这种速度行驶时,飞船将水推开,然后在其弓箭后面的槽中行驶。为了比这种位移速度更快,工艺必须足够轻,并具有“安装”波浪和“平面”在水中的力量。因此,要达到超过流离失所的速度,需要进行轻型构造。几乎不可能设计一种可以飞机的10m工艺品,甚至很难建造一个可以做到这一点的20m工艺,而在40m的情况下,仍然存在与钢重量相关的速度损失。GRP,纤维增强复合材料(FRC)和铝都是替代品。木材仍然使用,但仅在少数情况下使用。 客户偏好或偏见也是重要的驱动力。每个船主都有明确的视图,通常与以前的不良经历或先入为主的图像有关。FBM Marine听到了有关潜在客户为何指定特定材料的所有原因,即使它不是订购船只的最佳材料。在这种情况下,改变所有者的想法是困难的,但是如果提出好的技术或生命周期成本的论点,则可能是可能的。以下是在海洋环境中使用各种材料的一些论点。亚博网站下载 Welded Aluminium Hulls焊接的铝制船体变得越来越流行,因为该材料具有许多优势,并且具有轻量级。曾经有很大的偏见反对在海洋环境中使用铝,但是如今,专门为船只和快速渡轮(长达120m)生产的铝吨位正在迅速增长。使用的合金通常为5083(板)或6082(挤出),在美国使用6061。 Advantages and DisadvantagesHowever, the marine environment is particularly harsh for any material, and aluminium has two Achilles’ heels, low fatigue strength and low position in the galvanic scale, figure 1. On the other hand it does not rust or suffer osmosis, and paint coatings last longer than on steel. Aluminium internal areas need no protective painting, and many craft are left unpainted externally above water. The surface goes gritty but the degree of corrosion is small.
|
图1。Deep Pitting corrosion in an aluminium alloy after only a year in service in a marine application. |
铝的低疲劳强度在众多船只中引起了问题,从巡逻艇和快速渡轮到大型衬里的上层建筑。出现问题是因为,在干燥的空气中,铝合金表现出与大多数金属,焊接结构以及浸入海水中的疲劳强度相同的疲劳强度比,疲劳强度降低。这意味着设计人员必须将压力限制为低至30-40 MNM-2. As a result of this reduced fatigue strength, the bottom aft structures of waterjet-powered fast ferries have suffered from extensive fatigue cracking. Similarly, the waterjet inlet tunnels, figure 2, are subject to intense vibration as they are very close to a multi-bladed impeller that sends pressure pulses through the water. On top of this, the impeller is usually made of stainless steel and galvanic effects can wreak havoc, even when the impeller is stationary.
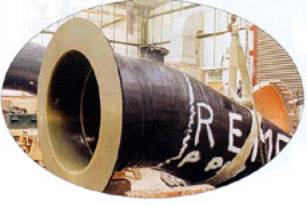
|
Figure 2.一条纤维增强的复合水剥水隧道,该隧道克服了与铝隧道相关的疲劳破裂,电腐蚀和腐蚀等问题。 |
Passenger Safety然而,铝是快速渡轮的主要材料,因为唯一提供必要性能的其他材料是GRP或FRC。亚博网站下载乘客的安全是塑料的关键问题。GRP结构可以包含火,但是所产生的烟雾和有毒的烟雾也可能是杀手。快速渡轮现在受到最近推出的国际海事组织安全守则的约束。以前的代码仅允许使用非燃烧材料(该定义中包括铝),但是新代码定义了所谓的“限制材料”的标准亚博网站下载。这些包括在ISO房间角测试下进行烟雾,毒性和热量释放的限制。 Not many normal plastics pass this standard. Phenolics do, but they have serious drawbacks for producing large structures in the marine industry the need to post cure at elevated temperatures, the health hazards during production and their lower mechanical properties. There are one or two new products that pass the standard but their applicability extends mainly to internal outfitting, such as linings and ceilings. This does mean, though, that the passenger saloon can be made to look more attractive more in the style of an aircraft. Aluminium Honeycomb Structures
铝制蜂窝状由铝皮制成,上面覆盖着薄薄的装饰塑料层压板,也广泛使用。此“复合材料”用于各种厚度,用于较小的舱壁和衬里。行李储物柜和天花板可以用酚类皮肤和铝制蜂窝状成型,看起来与飞机相同。该材料的铝芯被归类为不可燃烧的,因此不必通过ISO测试。 The Future for Plastics很少有快速渡轮完全从塑料到新代码建造。实际上,目前不太可能进入市场。因此,解决方案是设计一个容器,以防止通过用防火材料(例如岩盘)覆盖所有内部表面,从而防止大火到达塑料结构。亚博网站下载这并不能高高提高成本,因为无论如何,乘客住宿,汽车甲板和驾驶室的所有表面都必须被热隔离,并且可以将Rockwool用于两次工作。但是,对于大于20m的塑料飞船来说,高工具成本是一个问题,因此铝不太可能在几年内被取代。 Aluminium Extrusions铝也被广泛用于大型挤压形式,用于主要的结构应用。整个甲板是由带有整体T加齿剂的挤出木板制成的。FBM Marine also use box section extrusions for creating a `raft' to which the two hulls of a catamaran are welded, figure 3. Quick to produce, the extrusions need no internal inspection in service, and the ‘honeycomb’ produced gives the catamaran substantial built-in buoyancy. The largest extrusions used are 300mm deep and 12m long. These are laid alongside each other and automatically welded together to create a deck section 12m by 4m. These welded extrusions are the only part of the structure holding the two hulls together.
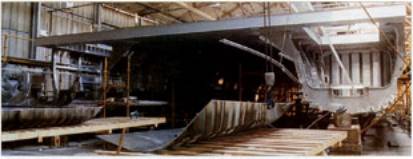
|
Figure 3.长度水平挤出是焊接在一起的挤压巢的一段,以形成乘客双体船的甲板。 |
Hybrid Structures海洋结构的新兴趋势是,使用不同材料的组合正在越来越多地使用。亚博网站下载“混合动力”一词用于描述这些组合,而不是旧词“复合”,这今天暗示了塑料和增强的组合。(不久前,“复合材料”一词是指带有木板的钢制框架。)混合结构主要由铝制成,GRP或FRC在更合适的区域使用。例如,FBM Marine通过将其从实心GRP模架中制成,并使用不锈钢螺栓和粘合剂密封胶将其从实心GRP造型中解决,从而解决铝喷气隧道的问题。 Geometric ConsiderationsThe problem of rapid double curvature can also be solved using moulded GRP. FBM Marine recently built two small waterplane area twin hull (SWATH) vessels for the Ministry of Defence, which have torpedo-shaped hulls, figure 4. The cylindrical part of the torpedo shape is easy to make in aluminium, but the nose cone is very difficult. So instead, these were moulded in GRP and flange bolted to the aluminium cylinder to create a hybrid hull. The cones were filled with foamed-in buoyancy in order to achieve the damage stability required. Foam filling an all aluminium structure would not have been allowed by the classification authorities, because access to the internal structure for regular inspection would not be possible.
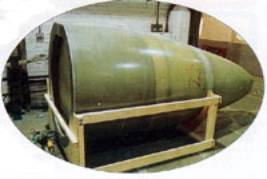
|
Figure4.A fibre reinforced composite nose cone of a small waterplane area twin hull (SWATH) |
Foam Sandwich PanelsFRC的泡沫三明治面板可以取代其他区域的铝。那些避开乘客轿车或汽车甲板的船只的那些部分不受这些区域的严格火灾法规的约束,因此可以使用夹心形式的大型FRC面板。这些提供了比铝的优势。焊接形式中的铝结构比钢遭受焊缝失真和收缩。船体通常比设计短几英寸,但真正的问题是美学之一。屈曲面板难看。 One customer demanded that FBM Marine create a smooth surface over an entire superstructure area. The solution was to build an aluminium ‘box’ that formed the structural and fire integrity of the saloon and then to clad it with FRC panels. These panels were lightweight foam sandwich panels with very thin skins of stitched cloth and polyester resin. The resulting superstructure finish was yacht-like. 船体中的结构粘合剂Another way of reducing the unsightly effects of distortion is to join aluminium panels together using structural adhesives. In fast ferry design, the problem with adhesives is their poor resistance to collapse in a fire. The solution is to combine rivetting with the adhesives. Panels are very large and in many cases need assembling vertically, so rivets are required in any case just to hold the surfaces together while the glue dries. However, rivet spacing can be much greater than in a rivet-only joining process. Applications of Composite MaterialsAnother positive trend for composite materials is the increasing replacement of steel shafting with composite shafts. Carbon fibre composites are the best materials for this application. Shaft diameter is greater using composites, but the weight is a fraction of steel shafts. Other parts that are being made from moulded reinforced plastics rather than metal include double-skin doors, shower trays, Bimini sun shields for tropical waters, navigation light boxes, wheelhouse consoles and chain cable lockers. SummaryHowever, the marine construction world is very conservative. Sandwich bottoms for boats are still frowned upon, as there have been too many disasters in this area. In fact, sandwich decks and superstructure roofs still give delamination and blistering problems, especially under tropical skies. Part of the problem lies in lack of quality control during construction, but sun, sea and salt water combine to create a very harsh environment for any material. Clearly, for a material to be successful in marine applications it must prove itself equal not only to competing materials, but to the challenges posed by nature. |