Starting up a new process typically involves a series of iterative changes to process settings until the particle size (blue line) is within the required specification (dotted orange lines).
Figure 1.Graph to show how changes in process settings affect particle size.
These iterations are necessary when using off-lineparticle size analysis techniques。随着任何过程的更改,随着过程达到稳态(绿色圆圈),在进行采样(红色圆圈)之前都会延迟。等待在实验室中完成的离线测量并传达给工厂操作员的结果。
In the above example, which used off-line measurement techniques, it took 50 minutes to achieve the required particle size - defined as a series of two successive in-specification measurements.
Milling Start Up Using On Line Particle Size Analysis
Using in-line, real-time particle sizing there is no requirement to wait for steady state conditions or to rely on results arriving from elsewhere. Process changes can be implemented immediately and dynamically to ensure that the desired particle size is achieved as quickly as the processing equipment will allow.
In the following example the process was brought within specification in under 8 minutes.
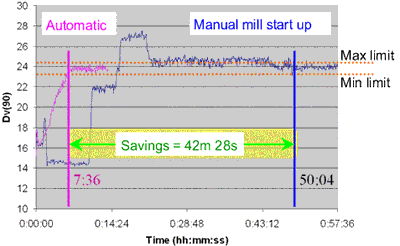
The resulting 40+ minutes decrease in processing time reduces the need to store, reprocess, or downgrade the out-of-specification material, and reduces the amount of energy consumed in 'tuning' the process.
.png)
This information has been sourced, reviewed and adapted from materials provided by Malvern Panalytical.
For more information on this source, please visitMalvern Alachytical。