将三种油分析技术应用于在测试电池中运行的发动机中使用的油样品。这三种技术是自动磨损颗粒形状分类,传染性和光谱学。将来自该技术的分析结果进行了比较,以确定其在单独或组合中的工作效果,以便基于油分析快速确定发动机状态。
本文的详细信息和评论从三种技术在540小时发动机运行的分析结果。共有31个样品取从开始到结束。所有样品与原子发射光谱仪进行分析,为21的元素分析结果的记录。相同的样品,以获得颗粒分布和颗粒形状的分类信息与所述LaserNet罚款-C颗粒形状分类进行分析。Ferrograms进行期间的磨合,稳定的磨损和朝向发动机试验结束用于与从键油样品的光学显微镜形态学分析准备。
三种技术之间的汇总数据显示良好的相关性。每个本身能够识别磨损的趋势。然而,从实际的观点来看,该数据表明,与光谱自动磨损颗粒形状分类相结合,提供一种快速的方法来确定详细的发动机状态,并且可以作为一种筛选工具一起使用,以开展铁谱分析之前需要。
介绍
这项研究的目的是在他们的能力三种分析方法的相关调查,以确定所使用的油样磨损的趋势。的发动机制造商共有31个用过的油样品从用于此目的的测试单元提供。用于分析油样品的三个器械是一LaserNet罚款-C(LNF-C)颗粒形状分类和粒子计数器,一个Spectroil M / C油液分析光谱仪,和一个铁谱T2FM实验室。第二个目标的测试程序的是评估LNF-C的形状识别特征,并将它们与铁谱的使用T2FM Ferrogram设备和光学显微镜的更常规的词素解析技术。
LaserNet Fines-C是一种台式自动油屑分析仪器,如图1所示。它使用激光成像技术和先进的图像处理软件,通过测量尺寸分布、进展速度和速度来识别机械故障的类型、生产率和严重性,润滑油或液压油中磨损碎屑的形状特征。LNF-C在分析前不需要任何特殊样品制备,也不需要电极或气体等耗材。
图1. LaserNet-C
本报告中油样的总分析时间约为每个样品2.5分钟。铁谱实验室(图2)由T2FM铁谱仪和双色显微镜组成。铁谱仪用于将用过的油样中的磁性和部分磁性颗粒分离到基板上,以便专家可以通过双色显微镜观察并作出解释。yabo214总的样品制备和分析时间从每个样品15分钟到30分钟不等。
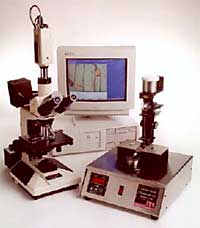
图2。T2铁谱分析技术实验室上调频
的Spectroil M / C油液分析光谱仪是基于所述旋转圆盘电极(RDE)技术台式原子发射光谱仪,图3,提供磨损金属,污染物和添加剂在润滑剂和液压流体的同时分析。在这些测试中使用的仪器是能够提供21种元素的分析结果,没有任何特殊的样品制备的。本报告中的油样分析时间是每个样品约1分钟。
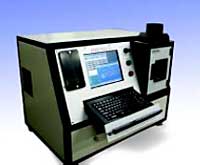
图3。Spectroil M/C石油分析光谱仪
过程
使用LNF-C和Spectroil M / C 31个的所有样品发动机的完整病历进行分析。从LNF-C结果,从该组特定的样品被选择用于使用T2FM Ferrogram设备和光学显微镜一个更深入的形态分析。由于样品保存了几个星期,他们第一次彻底为了得到任何颗粒再次悬浮使用自动震荡器中震荡。yabo214所述样品也通过手摇动之前将其与每个仪器的分析另一个30秒。将样品也被放置在外部超声波浴45秒,以除去之前将其与所述LNF-C分析气泡。
结果
用这三种仪器收集了大量的数据。有些是多余的,有些是毫无意义的;然而,通过对31个样品进行540小时的分析,大多数分析结果很好地了解了测试单元中发动机的机械健康状况。图4是LNF-C趋势特性的屏幕截图。它显示了31个被分析样品的总粒子数的趋势。yabo214曲线显示了一个“浴缸”形状,这是一个典型的磨损周期在一个特定的机器的生命周期。磨损阶段是击穿,然后是正常的稳定磨损,最后磨损到失效。
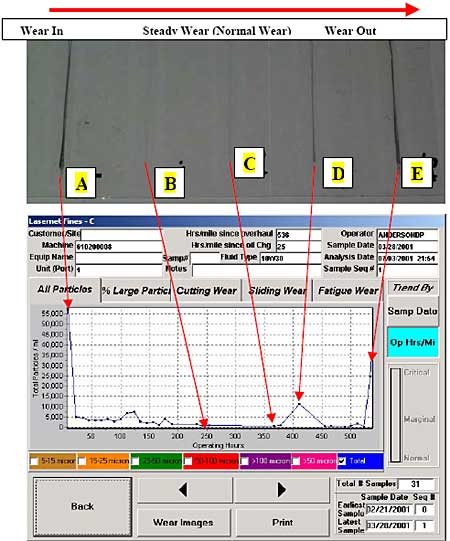
图4。磨损周期的不同阶段由LNF-C和铁谱图描述
从试验的不同磨损阶段的不同油样制备了铁谱图,如图4中的A到E所示。铁屑在各种铁谱图上的沉积与LNF-C给出的定量结果有很好的相关性。两者之间的比较如图4所示,实际的铁谱图与LNF-C所确定的趋势相比较。
Spectroil M/C油分析光谱仪分析的21种元素中,只有5种元素表现出磨损和磨损趋势;其余元素要么是添加物,要么以不显著的浓度存在。铁、铝、铜、硅的分析结果如图5所示。叠加的字母是用来描述铁谱图的测试槽小时数。
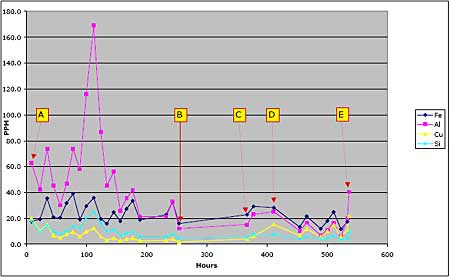
图5。光谱分析趋势
我们不知道在测试细胞上进行的测试类型,但在540小时的操作中,该油完全改变了至少15倍。从未允许留在发动机超过33小时,并在450到500小时之间进行每10小时更换一次。在每个元素的趋势中,从谷谷(低浓度点)中的油变化是明显的。
制作和分析铁谱的五个测试阶段(编号为A至E)将用于显示三种分析技术之间的相关性。
样品A - 8.8发动机小时-磨耗
磨合期间的LNF-C磨损汇总结果如图6a所示。检测和计数的大于4ìm的颗粒总数为57278/ml。大于20ìm的颗粒数量显示在切割、严重滑动、疲劳和非金属磨损类别中。这些粒子轮廓的yabo214LNF-C图像图如图6b所示。LNF-C鉴定并在磨损总结中量化的大部分大颗粒是严重滑动和疲劳颗粒。如图6c所示,铁谱通过数字照片证实了这一事实。图6c所示的第一个颗粒是严重滑动磨损的一个极好例子,清楚地显示了表面上的特征滑动痕迹(平行线)。如图5所示,样品A的光谱油分析显示铝、铜和硅的磨损金属水平较高。磨合过程中不会出现极高浓度的磨损颗粒,因为这些颗粒往往大于RDE光谱学的10ìm粒径检测能力。这一事实在粒子图像图和铁谱图中得到了证实。
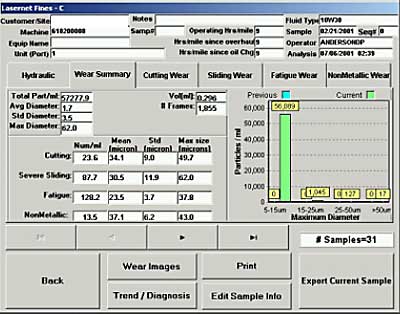
图6 a。LNF-C磨损总结屏幕,8.8小时
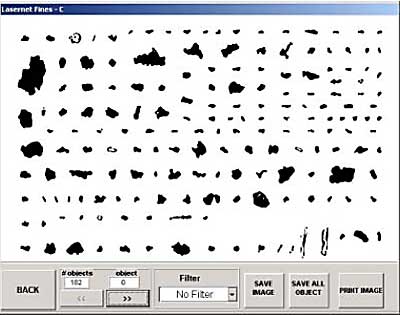
图6B。LNF-C粒子图像映射
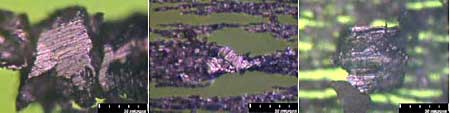
图6C。铁谱照片显示了在闯入过程中严重的滑动磨损
样品B.- 254发动机小时 - 正常运行(轻微磨损)
运行254小时后LNF-C磨损汇总结果如图7a所示。检测和计数大于4 ìm的颗粒总数降至107yabo2140 /ml。大于20um的颗粒数显示在切削yabo214、严重滑动、疲劳和非金属磨损类别中。这些粒子的粒子轮廓的LNF-C图像映射如图7b所示。yabo214这些结果与正常的磨损模式一致,预计在磨合期和数次换油后,磨损颗粒会减少。yabo214图7c所示yabo214的颗粒是由剪切混合层的脱落引起的正常滑动磨损产生的摩擦磨损的很好的例子。摩擦磨损颗粒通常是大小从5ìyabo214m到0.5 ìm或更小的血小板。它们表面光滑,通常厚度小于1微米。LNF-C和铁谱检测到的偶然和随机的大磨损颗粒被认为是正常磨损过程的一部分。如图5所示,样品B的油光谱分析证实了磨损金属的低浓度。
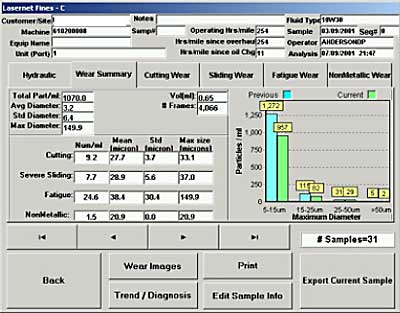
图7。LNF-C磨损摘要屏幕254小时
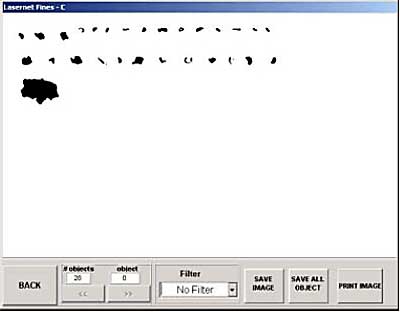
图7 b。LNF-C粒子图像映射
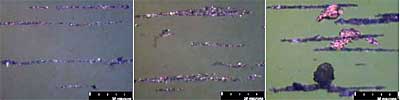
图7 c。照片显示正常运行时细微的摩擦磨损
样品C.- 366.7发动机小时-正常运行(轻微磨损)
在366.7小时的操作之后,LNF-C磨损总结结果如图8A所示。检测到且计数大于4μm的颗粒总数仍然非常低yabo214下去至745 / ml。大于20μm的颗粒的数量可忽略yabo214不计,如切割,严重滑动,疲劳和非金属磨损类别所示。这些颗粒的粒子剪影的LNFC图像映射如图8B所示。yabo214与样品B一样,这些结果与正常磨损模式一致,并且一个人期望在突破时段后磨损颗粒减少和几种油。yabo214Ferrograms,图8c,也证实了大多数正常的摩擦磨损颗粒,偶尔的较大颗粒。yabo214
样品C的光谱油分析(如图5所示)证实了磨损金属的低浓度。
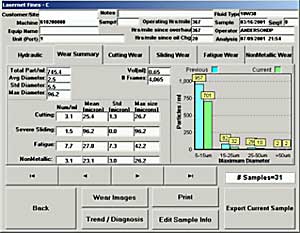
图8。LNF-C磨损汇总结果
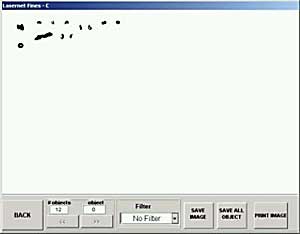
图8 b。LNF-C粒子图像图
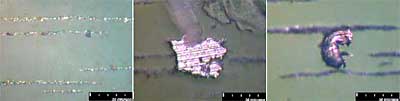
图8 c。照片显示精细摩擦磨损和偶尔的较大粒子
样品D.- 411.3发动机小时-开始磨损
运行411.3小时后的LNF-C磨损汇总结果如图9a所示。检测和计数的大于4ìm的颗粒总数增加了10倍以上,达到11367/ml。如严重滑动、疲劳和非金属磨损类别所示,大于20ìm的颗粒数量也大幅增加。这些粒子yabo214轮廓的LNF-C图像图如图9b所示。LNFC结果证实了磨损过程的增加,从该样品制备的铁谱图也证实了这一点。与样品B和C相比,细摩擦磨损显著增加,如图9c所示,更频繁地出现大的滑动和疲劳磨损颗粒。
样品D的油光谱分析如图5所示,通过铁、铝、铜和硅等磨损金属浓度的增加,证实了磨损模式的增加。
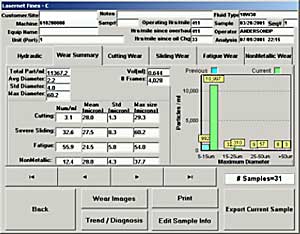
图9。LNF-C磨损汇总结果
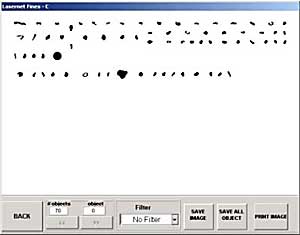
图9 b。LNF-C粒子图像图
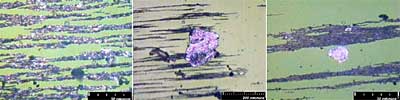
图9 c。照片显示摩擦磨损,大型严重滑动铝颗粒和大型铝疲劳薄片
样本E.- 534发动机小时-磨损
运行534小时后的LNF-C磨损汇总结果如图10a所示。检测和计数的大于4ìm的颗粒总数增加了一倍多,达到24493/ml。如严重滑动、疲劳和非金属磨损类别所示,大于20ìm的颗粒数量也急剧增加。疲劳颗粒的增yabo214加和大量是特别值得关注的。对粒子轮廓的LNF-C图像图进行电子过滤,以仅显示疲劳粒子,图10b。
请注意,LNF-C罚金分析粒子的轮廓形状,即它们的“轮廓”。yabo214结果是通过计算轮廓到一个复杂的神经网络模式识别算法产生的,该算法已经训练使用实际已知的磨损粒子轮廓。切削磨损、疲劳磨损和滑动磨损颗粒由斯旺西大学的试验装置制造,收集的颗粒用于训练LNF磨损颗yabo214粒识别软件。由于LNF- c内部的光学系统使用透射光(背光),LNF无法区分粒子颜色、纹理或表面属性。当进行磨损颗粒类型分析时,这些都是需要考虑的重要属性。因此,每个磨损类别的结果仅是那种典型的颗粒的剪影。这类似于只用透射光在光学显微镜下观察粒子。yabo214
还应该提到,应该提到其他类型的颗粒如二硫化钼,碳薄片和暗金属氧化物,如果它们存在于样品中,将根据其yabo214形状进行耐磨损类别的磨损类别之一。.阻挡光的任何粒子将被分类为三种金属粒子类别,即滑动,疲劳或切割之一。
由于这是一个往复式发动机,但是并不预期会有在滚动接触许多表面在球轴承或齿轮齿发现,将能够产生真疲劳颗粒如的。yabo214相反,绝大多数列为由LaserNet罚款“疲劳”颗粒根本没有足yabo214够长的被归类为滑动磨损颗粒。由铁谱颗粒表面的检查表明,米任何颗粒显示表面条纹,如在图6c和8c,即使颗粒不大于宽度长得多。yabo214当在疲劳类别LNF-C放颗粒因为LNF-C只依赖于轮廓图像,必须小心。yabo214
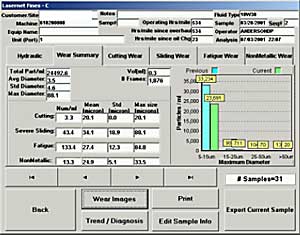
图10a。LNF-C磨损汇总结果
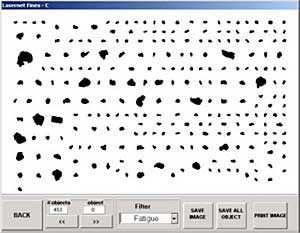
图10B。LNF-C粒子图像映射
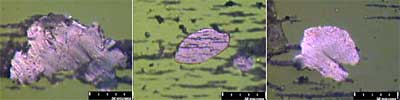
图10c。显示大疲劳粒子的照片yabo214
磨损过程明显增加,样品E的光谱油分析(如图5所示)也通过增加铁、铝、铜和硅的磨损金属浓度确认了增加的磨损模式。尽管光谱测定技术无法挥发,因此无法分析LNF-C和铁谱仪检测到的大磨损颗粒,但也会产生足够小的磨损颗粒,以对导致磨损过程的实际金属进行定性和定量分析。yabo214
讨论
发现LNF-C结果在更传统技术的定量和定性方面,即传导性和光谱分析的定量和定性方面非常一致。LNF-C的形状识别特征显示出在突破和发动机操作的最后小时内疲劳和严重滑动碎屑的大幅增加。虽然通过这种方法确定碎片的性质和来源是不可能的,但它肯定会根据专家分析师提供详细的冰文分析。
5个样品的铁谱分析清楚地表明,与LNF-C结果相比,总体粒子数和更详细的粒子类型都很好。铝颗粒很容易用铁谱鉴别,因为yabo214它们是非铁的。与铁粒子不同的是,非铁材料将随机yabo214沉积在铁谱的长度上,而不必使其最长的边穿过亚博网站下载铁谱的宽度。与其他碎片yabo214相比,这些粒子看起来也非常明亮,可以从本报告提供的一些粒子图像中看到。
样品的光谱分析由于异常高的油变化频率而变得更加困难;然而,在整个试验过程中,与LNF-C数据和铁谱相一致的磨损金属趋势仍然很明显。获得了良好的相关性,证实了磨合过程中磨损增加,正常运行过程中磨损减少,再次向发动机磨损方向增加。原子发射光谱在精确量化磨损金属浓度大于10ìm的尺寸方面的局限性也被证明不会对预测磨损模式造成损害。
结论
制作铁闹钟并分析每个样本是不可行的,因为铁镜既耗时又昂贵。本报告证明了如何彼此结合使用自动粒子形状分类和原子发射光谱,并应用于选择性铁置分析的筛选工具。LNF-C可以通过脱离主体性并将其自动化到一个更详细的分析的点来补充二旋代。原子发射光谱可以提供元素分析趋势和有必要的信息,帮助确定磨损过程的原因,因此可以采取纠正措施来避免意外故障。

这些信息已经从AMETEK Spectro Scientific提供的材料中获得,审查和改编。亚博网站下载
有关此来源的更多信息,请访问AMETEK斯派克的科学。