多年来,渗碳一直是最广泛使用的工艺之一,以开发坚硬,耐磨层的钢组件。在渗碳过程中,流化床炉已被证明是非常有效的。虽然常规气氛渗碳可以在流化床中进行,但升压/扩散技术是首选,其周期在920°C至1000°C之间进行。在升压期间,富集的烃类气体会超过所需的碳势。这种富集的碳氢化合物通常是天然气或丙烷,并与载气(如氮气)混合以稀释碳氢化合物。因此只有氮存在,而被吸收的碳扩散到材料的核心。碳吸收速率受炉内碳势、钢的表面活性和溶解度控制,而扩散速率受菲克斯定律控制。与真空和等离子渗碳一样,表面碳和有效渗碳层深度可以通过计算机程序计算得到最佳时间。 使用流化床炉的优点使用流化床获得了许多优点。流体床和常规炉中的渗碳之间的主要区别是在升压时段期间流化床中产生的极高的碳电位。研究表明,在将烃气体传递到炉内的几分钟内,它已经破裂以产生游离碳颗粒,导致床达到高碳电位。yabo214因此,由于这种原因,流体床中的处理时间可以明显短于传统的熔炉。流体床的其他优点包括良好的温度均匀性和优异的传热性能,转化为更好的过程控制和均匀性。 的控制碳剖面的重要性然而,即使有了最新的炉技术,制造商往往不确定什么是最佳的外壳性能。很明显,在表面硬化的部件上,碳剖面是产生最佳性能和性能的关键。事实上,通常是碳的形状决定了最终处理部件的显微组织和硬度形状。例如,如果表面的碳含量过低,那么由此产生的硬度和耐磨性就会随之变差。相反,过高的碳含量会导致残余奥氏体过多,并在晶界形成碳化物网络,从而导致过早疲劳失效。 硬度和碳含量n梯度被认为是特别理想的是一种相对高的表面硬度,其延伸到生产被称为扁平硬度曲线的钢中。这种类型的硬度曲线可以提供许多优点。首先,与标准硬度轮廓相比,更平坦的轮廓在相似深度处具有更高的硬度值,因此改善了部件寿命的耐磨性。此外,已经表明,较高的碳水平可导致在已经显示出改善耐磨性的晶粒中形成的小球状碳化物。其次,在壳体硬化后,大量的碳碳组件是加工的或研磨,以使它们恢复到操作公差内。在最终加工或研磨过程中,从部件中除去高达0.2mm的材料是常见的。这种做法的问题在于,在典型的情况下,高达1.00mm的典型深度,这是拔出20%的硬化区,一旦移除底层表面具有相当较少的碳,因此降低硬度和耐磨性。考虑到这些点,重要的是建立升压和漫射时间之间的正确比率,以获得在淬火时产生所需的转化序列和壳体深度的碳梯度。 脉冲增强扩散技术试验表明,仅仅增加升压周期以获得更高的碳水平,就会导致过量的残余奥氏体和/或碳化物网络。然而,有一种替代标准渗碳循环的方法,可以更好地控制最终的碳分布。这种技术被称为脉冲增强扩散技术(PBD)。关键是要缩短助推和扩散周期,但在同一温度下,在一个周期内多次重复。这确保了高水平的碳保持在增加的深度,因此产生了一个平坦的硬度剖面。这种技术的另一个优点是,小的球状碳化物可以在高碳水平的组织内成核。 案例研究- 9310钢的脉冲扩散强化处理因此进行了一系列实验试验以评估脉冲升压漫射处理的有效性,并确定是否可以获得优异的碳和硬度曲线。样品材料是9310,一种常用的碳钢,并且在试图实现较高的碳水水平时可以提供困难,其由于高镍含量(高达3.55%)作为保留的奥氏体稳定剂并引起过量的碳化物网络。 实验的程序所有试验都是在950°C的流化床炉中进行的,使用天然气作为富集气体,高纯氮气作为载气。所有样品都是在93 10巴斯托克加工的。 标准推进和扩散渗碳循环第一次测试(循环1)涉及进行标准升压和漫反射循环,以获得1.00mm的有效壳体深度。基于Harris方程的计算机程序用于确定升压和漫射时间。计算出需要47分钟的升压期,然后是113分钟的漫射时间。完成碳碳循环后,样品是直接油淬灭,然后在180℃下发热。最后,在液氮中低温处理每个样品以转化任何保留的奥氏体和第二次发育。该标准循环不仅进行评估结果,而且还用于作为可以进行比较脉冲升压漫射循环的标准。 脉冲增强扩散渗碳处理周期实验的第二阶段是进行脉冲增强扩散处理。这最初包括将标准周期划分为较短的增强和扩散周期,并重复这些周期若干次。第一个脉冲推进扩散周期是15分钟的推进和25分钟扩散重复4次,产生的总周期时间与标准周期相同。第二个FBI循环将促进周期缩短到10分钟,并将扩散周期延长到30分钟,同样重复了四次。与标准循环一样,这些样品经历了初始回火,然后是零度以下的处理和渗碳后的最终回火。值得注意的是,为了使有效病例深度保持在1.00mm,总治疗时间保持不变。所有其他变量,如淬灭速率保持不变。试验结束后,每个试样被切割,安装在环氧树脂中,蚀刻和微观结构检查。最后,对每个试样进行横向硬度测试,以确定其硬度分布。这是在维氏显微硬度计上进行的,负载为100g。 A summary of the cycles carried out is given in Table 1.
|
1 |
950 |
47 |
113 |
1 |
油 |
脾气,冰冷,脾气 |
2 |
950 |
15 |
25 |
4 |
油 |
脾气,冰冷,脾气 |
3. |
950 |
10 |
30. |
4 |
油 |
脾气,冰冷,脾气 |
结果绘制硬度与深度清楚地表明循环之间的差异,并最终提供所产生的最终碳型材的指示。各个循环结果的图形表示如图1所示。
|
图1所示。9310钢经各种渗碳处理后的硬度分布。 |
强化和扩散处理的硬度曲线
标准渗碳循环(循环1)导致表面硬度为700HV,仅在100微米后开始逐渐下降,芯硬度为380HV。有效渗碳层深度约为0.9mm(在500Hv时确定。标准循环的显微组织以回火马氏体为主,少量分散的碳化物。 硬度P.用于脉冲升压漫射处理的roofile由两个脉冲升压漫射循环产生的硬度谱相似,然而,这两者都与标准循环产生的两者相似。与标准处理相比,循环2和循环3均具有高表面硬度(760HV)。这种更高的硬度保持在0.3mm的深度,因此在大约0.8mm的扁平型材中产生扁平硬度曲线,使得所有三个型材聚集在一起,以在0.9mm和1.00mm之间提供有效的壳体深度。在所有情况下,核心硬度在360和400HV之间。 微观结构的差异两种脉冲增强扩散周期的主要区别在于微观结构。在这两种情况下,基体均由回火马氏体组成,但循环2产生了具有强晶界碳化物网络的组织。然而,循环3产生了显著的微观结构改善。虽然有一些较大的碳化物存在,但它们分布均匀,在晶界没有碳化物网络。图2显示了每个循环产生的微观结构。
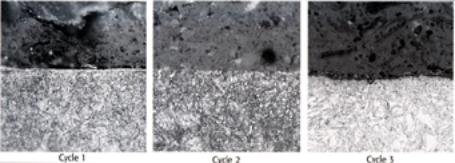
|
图2。9310钢经各种渗碳处理后的显微组织。 |
讨论修改标准渗碳循环以改变碳水平和形核球形碳化物并不是新技术。事实上,碳化物分散渗碳法最早是由O.E. Cullen在1961年提出的,并在此后的许多论文中都有涉及。然而,这些方法要求有第二个炉,以便在升压周期完成后在较低温度下使碳化物形核。这种技术虽然成功地生产了较高的硬度值和晶间碳化物,但在热处理行业并不实用。因此,脉冲增强扩散循环的一个主要优点是,它可以在一个温度下在单个炉中不间断地进行,并且通过现代可编程控制器,该循环可以在最小的监督下进行。 T.的影响硬度的处理周期通过对比实验结果,可以清楚地看到,脉冲增强扩散技术有能力产生一个优越的碳型材,并随后改善硬度型材。如图1所示,循环2和循环3都达到了较大的表面硬度和相当平坦的轮廓,硬度一直保持在增加的深度。事实上,脉冲增强扩散周期都保持700HV或以上,高达0.3毫米内的情况。这种类型的型材将提供优良的耐磨性的组件,并大大延长使用寿命。这也意味着渗碳后的任何磨削或加工对案件的不利影响将会更小。值得注意的是,这三个循环产生的有效表壳深度非常相似,超过0.7mm后,所有硬度值都大致相同。这意味着Pulse Boost Diffuse循环可以在不延长标准治疗时间的情况下进行,并且可以在关键部件上实现控制病例深度。 微观结构对材料性能的影响亚博网站下载微观结构对9310的最终性质的影响也相当重要。同样,微观结构强烈依赖于碳含量并实现最佳梯度。较低水平的碳不易检测,但会降低淬透性和耐磨性。过量的碳具有更明显的效果。过量的碳可以首先导致保留的奥氏体水平不可接受。在试验中,所有样品进行所有样品进行分类治疗,以便最小化保留的奥氏体,但必须考虑保留奥氏体的影响。当含量小于30%时,保留的奥氏体通常不被认为是有害的,特别是如果在一些情况下,则需要少量的保留奥氏体。 然而,在诸如严重装载齿轮的其他应用中,保留奥氏体限制为小于5%,因为奥氏体不稳定并且可能导致较低的硬度,降低耐磨性和过早失效。 过多的二氧化碳过量的碳还会产生晶界碳化物。随着碳含量的增加,碳化物开始勾勒出奥氏体晶界。如果这些水平继续增加,碳化物不仅尺寸增大,而且沿晶界形成网状结构。大颗粒碳化物在晶界处析出不利于冲击韧性和接触疲劳性能。这种情况在循环2中已经发生,而且似乎较长的促进周期已经导致一个可接受的碳水平。具有这种微观结构的部件很可能在使用中失效。还应该指出,9310的高浓度镍作为碳化物的稳定剂,这可能是碳化物在所有循环中都存在的原因。另一个需要考虑的因素是角效应的概念。大多数组件都有一个尖锐的边缘描述,这也可以加强有过量的碳水平的问题,因为碳从角落的两边扩散。然而,在敏感部件,这可能会造成问题,镀铜或停止油漆可能会使用尽量减少问题。 控制碳化物的形成然而,控制碳化物的形成可以带来好处。碳化物的体积、尺寸和分布对磨损性能有明显的影响。一般来说,由于碳化物合金的硬度很高,耐磨性随着磨损表面碳化物体积的增加而提高。因此,能够在表面硬化部件的显微组织内产生精细分散的碳化物是很重要的,例如循环3所产生的碳化物。 概括与传统渗碳炉相比,流化床炉渗碳有许多优点。在更高的碳势下操作的能力以及优异的温度均匀性和传热性能意味着改进的过程控制。很明显,通过改变渗碳循环来产生最佳的碳轮廓,表面硬化部件的最终性能可以显著改善。这已经用脉冲增强扩散(PBD)技术进行了说明,该技术成功地在钢的情况下保持了较高的碳水平,因此在硬度剖面和组织方面提供了相当大的改善。建议对PBD工艺进行进一步优化,以进一步量化该工艺的效益。 |