今天,英国的通勤者面临着延误,有时还会发生脱轨,因为铁路网络继续遭受着铁轨磨损和损坏的问题。2000年10月哈特菲尔德火车脱轨事件加剧了机械故障导致的铁轨断裂问题,近年来一直是头条新闻。 铁路FAI的原因饵哈特菲尔德的脱轨是由仪表角裂纹引起的。但这种形式的机械故障不是铁路轨道的唯一失败机制,尤其是可能遭受水进入的地下系统上的轨道。腐蚀,材料和环境技术集亚博网站下载团Capcis最近调查了一个铁路故障,这不是疲劳裂缝的结果。经过大量测试后,CAPCIS得出结论,由于硫化物应力腐蚀裂纹(SSCC)导致导轨失效 - 一种环保抗裂的形式。 检测和检查轨道相关硬件钢轨裂纹的检测通常包括对钢轨、卡箍、底板的目视检查,以及对钢轨头的超声波检查。这些检查主要集中在检测疲劳裂纹和钢轨磨损引起的重复接触列车车轮。直流牵引系统的腐蚀问题通常与杂散电流有关。电流从其预定路径“泄漏”可能会导致电流离开部件的轨道或其他设备的局部腐蚀。app亚博体育 案例研究-地下轨道系统的轨道故障在一个研究地下直流牵引系统杂散电流和其他腐蚀问题的项目中,CAPCIS被要求调查一个有点不寻常的轨道故障。事故发生后,现场拍摄的断裂钢轨照片显示,钢轨腹板严重变薄,导致超载失效。 初步检查然而,在收到钢轨断面和对断口的粗略检查后,很明显腐蚀和变薄不是故障的直接原因,如图1所示。
|
图1所示。失效钢轨的断口面。 |
详细检查对断口进行详细检查,未发现明显的疲劳开裂迹象,对轨头和腹板进行扫描电镜检查,仅发现脆性断裂。与钢轨头相比,钢轨腹板和钢轨脚表现出广泛的腐蚀,这表明这不是一个单一的事件断裂。 磁粉探伤为了检查是否有表面裂纹,用磁粉探伤对轨道头进行了检查。沿着钢轨磨损的轨距角发现了许多拉长的s形裂纹,如图2所示。这些裂缝被称为“头部检查”,通常长度为10毫米,但没有迹象表明故障起源于这些表面裂缝。
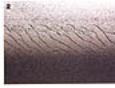
|
图2。导轨的头检查没有促成失败。 |
冶金检查然而,对断裂钢轨的腹板和底部进行进一步的冶金检查,发现了典型的由钢的氢脆引起的细裂纹,如图3所示。裂纹主要平行于断口,似乎与穿过钢的任何小的硫化锰夹杂物没有关联。
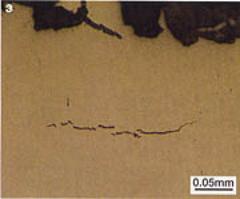
|
图3。断口金相检验显示,在钢轨腹板和钢轨脚处存在典型的阶梯式氢裂纹。 |
氢测试
质量制造钢的氢水平通常为1-2ppm。轨道幅度和头部的几个部分的化学分析显示出远高于现代轨道钢中预期的钢材升高的氢水量。在网的顶部记录2ppm的值,并且在网底部发现5ppm的值。发现增加的水平是环境氢吸收的结果。 环境tal检验在检查期间,有人指出的是,虽然隧道的某些地区显然是干燥的,但其他人在地方遭受了浇水。隧道环境也被发现是潮湿的,即使街道水平的环境温度有些冷却,也是如此。氢气的来源最终追踪到轨道旁边的停滞水池,发现用白色的“渣滓”覆盖。当干扰时,硫化氢气体(H.2S)可以立即被闻到,醋酸铅纸变成棕色,也表明它的存在。 化学测试为了确认失败的原因,在导轨上进行叠氮化试验(进行的化学试验,以确定材料是否暴露于含硫化物的环境),并将水样品返回到实验室进行测试.高水平的硫酸盐还原细菌(104在水中发现了每mL的SRB。SRB是微生物,其在水中化学减少水中的硫酸盐离子至硫化物。涉及的腐蚀反应H2年代生产单原子的氢气(H.0)在这一点腐蚀表面应该结合形成H2气体,但硫化物的存在阻碍或中毒这个组合反应使氢扩散到钢中。正叠氮化物测试和SRB的存在导致结论,钢轨几乎肯定是由于硫化物应力腐蚀开裂而失败。 硫化物应力腐蚀开裂SSCC最早于20世纪50年代在石油和天然气工业中被发现,并在相对较低吸收氢水平的高强度钢中出现。这种开裂形式高度依赖于钢的成分、组织、强度和总应力水平(应用和残余)——钢的强度越高,对氢脆的敏感性就越大。 失败之路氢裂纹的存在解释了断裂面上的腐蚀区域。随着时间的推移,小裂纹形成并增长,成为表面涌现,使裂纹面暴露于外部环境,进一步腐蚀和氢扩散。裂纹最终达到了临界尺寸,以致铁轨无法承受火车通过所引起的应力,并发生了脆性超载失效。 Sulp隐藏应力腐蚀裂纹及其消除虽然这种失败可能不是唯一的,但这是不寻常的。CAPCIS在石油和天然气行业中遇到了许多SSCC故障,但从未见过轨道部分的失败。过去,通过在轨道中的小氢裂纹开始的疲劳裂纹引起的轨道和螺旋椭圆形的氢有效失效,但是控制原制的氢水量在很大程度上消除了这些故障。 总结杂散电流腐蚀和疲劳裂纹的检测是相当直接的,而SSCC的检测对铁路工程师来说是非常困难的。现场叠氮测试是不切实际的和有效的超声检查锈蚀钢轨蹼和脚将需要广泛的清洗。大气H2可以闻起来,但源不是总是显而易见的。添加至此,SRB检测需要实验室测试,并且SSCC的诊断充满了实际问题。最大限度地减少导电到SSCC的条件风险的最简单方法是通过控制隧道环境和防止进水和停滞。 |