与传统电池相比,锂离子电池具有更高的能量和功率密度,因此在混合动力/全电动汽车(H/EV)、电动工具和便携式电子产品等领域有着广泛的应用。
采用电动汽车技术归因于两个主要因素;首先,与主要由ICU的低排放目标推动的传统内燃机相比,它们对温室气体排放的影响力低引擎达到2021年的95g / km那(米勒,2015)(Tsiropoulos I.,2018)。其次,是日益增加单次充电的续航里程至少是ICU发动机现有续航里程的一半以上。
这些因素更加强调细胞化学和细胞架构,电池组设计,加入和制造。因此,锂离子电池的选择取决于电池的化学性质,其化学性质直接影响到其使用的安全性、寿命行为、充放电时间和功率或能量密度。电池组由数百/数千个单体电池组成,提供H/EV汽车高效运行所需的电压和电流密度。
电池组和/或单个细胞的组装可以进行金相评估,以验证电池结构和化学物质。还可以评估用于制造包的各种连接技术。本文突出了可用于金相评估各种电池组件的程序。
样品制备技术
在切片之前,需要完全放电电池,并且没有可以存在标称电压。这是重要的,因为它最大限度地减少了与细胞短路相关的风险。锂电池应在干燥状态下切片,以避免与冷却剂的失控和随后吸收到细胞的层压结构中。阴极和阳极层压板中的活性成分由对水具有高亲和力的多材料组成。亚博网站下载这导致有害的腐蚀产品。
图片信用:Buehler
切片使用的是Isomet高速,借助于双鞍夹头的横截面。使用了一种有色金属磨料叶片。重要的是要确保安装在机器背面的提取系统,以解释产生的灰尘。
湿分切可以进行外部金属壳体而没有内部活性细胞元素的切片。焊接终点也用于湿截面。可以使用金刚石晶轮而不是磨料刀片,因为材料主要是金属(概要,2018)。亚博网站下载
.jpg)
图1用(a)表示Isomet高速的切片,(a)示出夹紧配置,(b)没有轧制电池元件的封闭壳体材料,(c)显示具有电池元件的电池,用于横截面图和(d)示出具有特征层压结构的段细胞。
图片信用:Buehler
越来越多的
锂离子电池可以在未安装和安装的配置中制备。未安装的样品应该准备好。为了便于处理,可以设计夹具夹具,以便在进行粗磨步骤时将横截面保持在适当位置。如果样品需要安装,应采用可浇铸的安装技术。作为环氧树脂的树脂是优选的,例如环氧基2或EPHothin 2,因为它们在固化过程中与电池组成元素的低反应性和低峰值放热温度。
可浇铸的样品完全适用于尺寸检查,电池盖组件焊接评估和终端焊接评估。这是因为该技术确保了焊接完整性而不会用压缩(热)安装过程(摘要,2018)发生的失真和/或损坏。
研磨和抛光
由于几种原因,应使用SiC文件进行细胞研磨。锂离子电池由具有不同耐磨速率和各种聚合物材料,金属组分和压实粉末的材料组成亚博网站下载。为确保良好的平面性和均匀的研磨,SiC文件提供最佳替代方案,不会对这些材料造成太多地下损坏。亚博网站下载
对于初始研磨步骤,建议使用细粒纸,只要它不会损害材料去除过程即可。如果需要高山去除,可以使用较粗糙的粗砂。然而,不应使用比P600(360粒)粗糙的粗糙。使用更精细的初始研磨的额外优点是需要更少的后续步骤。
为了确保更好地控制平坦度而不导致地下损坏,建议使用压板的每分钟的相对较低的转速干磨。在干燥研磨过程中,由于灰尘吸入的风险,必须考虑安全预防措施。使用防尘掩模和更低的压板速度显着最大限度地减少了与干式研磨相关的风险。使用该方法使用的过程制备安装的微微纤维。Buehler Ecomet 30.(摘要,2018年)。
表格1显示用于准备LiCoO电池的准备常规。这适用于其他类型的锂离子电池化学物质。
一步不。 |
表面 |
磨料 |
润滑剂/ 扩展器 |
力量 (每样本) |
时间 (分:秒) |
压换速度 (rpm) |
头 (rpm) |
1 |
SIC纸 |
P600. |
干燥 |
温和的 压力 |
直到飞机 |
120. |
手动的 |
2 |
SIC纸 |
P1200. |
干燥 |
温和的 压力 |
直到飞机 |
120. |
手动的 |
3. |
SIC纸 |
P2500. |
干燥 |
温和的 压力 |
直到飞机 |
120. |
手动的 |
4. |
SIC纸 |
P4000. |
干燥 |
温和的 压力 |
直到飞机 |
120. |
手动的 |
表2.显示用于制备电池壳体部件和电池组组件的焊接互连的准备常规。
一步不。 |
表面 |
磨料 |
润滑剂/ 扩展器 |
力量 (每样本) |
时间 (分:秒) |
压换速度 (rpm) |
头 (rpm) |
回转 |
1 |
SIC纸 |
P400. |
水 |
25 N. |
直到飞机 |
250. |
60. |
<< |
2 |
SIC纸 |
P1200. |
水 |
25 N. |
04:00 |
150. |
60. |
<< |
3. |
Policloth. |
3μm元 |
Metadi. |
30 N. |
04:00 |
150. |
60. |
<< |
4. |
Chemomet. |
0.05μmmastermet,0.05 MasterPrep |
水** |
25 N. |
02:30 |
120. |
60. |
>> |
显微镜分析
光学和电子显微镜技术均用于分析接收的细胞,切片细胞和微段。对于光学金相,使用尼康LV150直立显微镜,用于提供层压结构的详细视图。宏观架用于电池的光学/横截面。对于电子显微镜,使用FEI电子显微镜进行能量分散光谱(EDS)工作。
由于电池组件是导电的,未安装的样品是理想的电子显微镜工作,以确保良好的阳极和阴极区域的元素分析。传统的金相制备技术对无活性成分的胞外几何形状进行了研究。
细胞结构和描述
锂离子电池的内部电池结构由外圆柱形壳体构成,该外圆柱壳体保护锂金属氧化物阴极的内部活性电池元件,石墨阳极,有机溶剂和锂盐的电解质。内部电池结构对所有锂电池共用,并且主要变化是有源阴极/阳极化学物质。轧制元件容纳在外壳中(图2,A-E)。根据电池的最终应用,可以使用聚合物外护套(D和E),或者可以露出电池。后者为电池组装成电池组时,为电池提供理想的表面。
.jpg)
图2.图示了圆柱形固体锂离子电池的外壳结构,其具有具有(a)的聚合物护套,而显示阴极,(b)阳极侧和(c)是电池盖帽区域,(d)和(e)示出了聚合物外护套。
图片信用:Buehler
内部电池组分由阴极,隔膜和阳极层压板组成,其被缠绕为制造细胞元件。阴极端子连接到PTC(正温度系数)开关和电池盖,其具有内置的安全阀机构。这在图3中示出了。如果电池被异常使用,例如从电池的过度拉伸电流,使得PTC的导电聚合物加热并变得电阻,停止电流并用作短路保护。一旦冷却,PTC就会返回导电状态,这允许电池操作。
安全阀机构由膜密封件组成,膜密封件在高压下破裂并缓解细胞中的压力堆积。但是,这可能导致细胞泄漏并干燥。该问题已被使用可重新密封通风口的新设计减轻。安全值机制,PTC(正温度系数)元件和电池盖固定到电池的开口端。这是通过填充通过绝缘密封垫圈来完成的,从而密封电池内部,图3(a)。
.jpg)
图3.(a)帽(开放)端侧的电池横截面的示意图,示出了构成外壳的各种部件,以及(b)实际细胞横截面的图示。
图片信用:Buehler
另一方面,层压层环绕着金属中心线,中心线由阳极和阴极以及各自的活性元素组成,如图4。该阴极由位于阴极集电极两侧的阴极活性物质层组成。电流收集器由金属箔制成,可以是不锈钢箔、铝箔或镍箔。
.jpg)
图4.电池横截面,示出了由阴极和阳极,外壳和中心销的层压层组成的层压层。(b)示出了中心销周围的有源单元元素层的特写。
图片信用:Buehler
阴极的活性材料层由具有粘合剂,导电剂和陶瓷的配方制成。陶瓷是无机氧化物,例如SiO,Al2O, MgO, ZrO, TiO, NaO等氧化铝具有较好的锂扩散性能。活性正极材料包括锂硫化物,锂氧化物,或亚博网站下载复杂的含锂化合物,如锂磷酸盐化合物。这些化合物包括锂/镍氧化物(LiNiO)、锂/钴氧化物(LiCoO)、锂/镍/钴/锰氧化物(LiNiCoMnO)和锂/钴/锰氧化物(LiNiCoO)。
另外,它们可以是基于磷酸化合物,例如锂 - 铁 - 锰磷酸化合物(Lifemnpo)和锂 - 铁 - 磷酸化合物(Lifepo),图6.基于其功率和能量密度选择电池,生命时间和安全。汽车工业中最广泛使用的电池是Lifepo,钛合金,NCM和LiCoO。
导电剂由碳基材料组成,用于更好的电导率,例如炭黑或石墨。亚博网站下载粘合剂由氟基聚合物组成,例如聚偏二氟乙烯,聚四氟乙烯,聚偏氟乙烯和氟化物型橡胶。
阳极是夹芯层,由集电体之间的阳极活性材料层组成。阳极活性材料层由导电碳掺杂锂,例如石墨,并与在阴极层压上发现的相同材料结合,图7。亚博网站下载电流集电极由金属箔制成,例如镍或铜线圈。
层压结构可以光学评估,以评估阳极/阴极层材料的厚度,面积或体积分数。体积/面积分数分析可以对锂离子电池中活性材料的能量密度评估进行见解,图6.当电极厚度被建模为能量密度的函数时,发现能量密度在临界电极处具有最大点亚博网站下载给定放电率的厚度(DU,2017)。得出结论是,受活性材料锂离子扩散影响的限制因素是电池偏振和无效材料的未充分利用,以及在电解质相(YU,2013)中的耗尽。亚博网站下载
利用OmniMet图像分析软件对测量的面积/体积分数和厚度进行分析。该软件可以脚本执行覆盖的多条线阴极和阳极层,不管几何形状。为了深入分析厚度,该软件还将计算feret直径在各种角度(SumMet, 2018)。
.jpg)
图5.(a)上面的光学显微照片说明了细胞横截面图。图A示出了由阳极和阴极组分组成的外壳和交替的层压层,(b)表示朝向电池的离心百分点的结构。
图片信用:Buehler
.jpg)
.jpg)
.jpg)
图6.说明(a)阳极和(b)阴极层的活性物质面积/体积面积分析,和(c)显示相应的近似厚度。
图片信用:Buehler
.jpg)
图7.围绕阴极层压层的较高的倍率电子显微镜(EDS)分析显示其组成化学。显而易见的是,还拾取了残留的活性和粘合剂组合物。
图片信用:Buehler
.jpg)
图8.图示了锂离子电池的层压结构的较低放大倍率电子显微镜(EDS)分析,其中具有主要的构成部件元素图分析。显微照片清楚地突出了阳极(富含Cu电荷收集器和阴极层(富含钴)的阳极,用Al电荷收集器。
图片信用:Buehler
电池互连 - 焊接
加入或焊接技术是关键发展的领域。对低自放电,更高的能量密度以及电池组的可移植性的需求越来越大,作为H / EV的替代电源。通常,电池组由数百和/或数千个单独的锂离子电池组成,在系列或并行配置中连接。这有助于实现所需的能量和力量。
电池组可以是单个模块或多个模块,其串联或并联配置与容纳在壳体结构中的传感器和电池控制系统连接。模块和/或包装需要强大且可靠的互连。加入方法取决于细胞类型并维持使用中的良好机械,热和电气行为(DAS,Li,Williams和Greenwood,2018)。
电阻点焊、激光束焊和超声波焊是蓄电池组最常用的连接(焊接)方法。焊接参数和合成焊接面积需要高质量,同时不影响电池外壳的结构。对这些技术进行了研究,结果表明,激光焊接技术具有最低的电接触电阻,而超声和点焊技术显示了相当高的电阻,这是由于焊接技术中出现的缺陷(空洞)(Martin J. Brand, 2015)。
它的结论是,不同的加入方法具有不同的优点和缺点。例如,具有低电导率的关节伴侣,例如镀镍钢导体为18650个细胞,点焊是理想的连接技术。对于几乎所有电池单元连接,在焊接过程中夹紧焊接部件,超声波焊接是合适的。
然而,未挤出的电池配置的超声波焊接导致导体中的裂缝形成和电池单元的损坏。确定激光焊接是理想的,可用于更好的质量焊接,并且可以连接任何电池单元,与表面产生的危险因素有较少的风险因素(Steen,2010)。
在焊接试验中,采用点焊、激光焊和超声波焊连接空电池罐。如图9所示。它们是金相制备的,目的是识别影响电接触电阻的缺陷和/或研究其微观结构。由于铜具有高导电性,所以使用了由铜制成的互连样品。正如Zhou(2000)和Martin J. Brand(2015)所报道的,这在焊接过程中带来了相当大的挑战,很可能会出现焊接缺陷。
.jpg)
图9.锂离子电池具有左侧焊接,中间超声波焊接和右激光束焊接互连的锂离子电池的公共焊接技术,锂离子圆柱形电池(Martin J. Brand,2015)。
图片信用:Buehler
焊接准备
根据表3,焊接连接是半自动制备的。这是为了确保所有组分材料类型都是金相制备的。在图10中示出了激光焊接和铜互连的铜互连点焊接的金相部分。
表3显示用于准备LiCoO电池的准备常规。这适用于其他类型的锂离子电池。
一步不。 |
表面 |
磨料 |
润滑剂/ 扩展器 |
力量 (每样本) |
时间 (分:秒) |
压换速度 (rpm) |
头速度 (rpm) |
回转 |
1 |
SIC / DGD等效物 |
P400. |
水 |
5磅 |
直到飞机 |
250. |
60. |
<< |
2 |
SIC / DGD等效物 |
P1200. |
水 |
5磅 |
01:30 |
250. |
60. |
<< |
3. |
Policloth. |
3μm |
MetaDi流体 |
5磅 |
04:00 |
150. |
60. |
<< |
4. |
Chemomet. |
0.06μmmastermet. |
水** |
5磅 |
02:30 |
150. |
60. |
<< |
如图11 (A)所示,点焊连接件根部存在微/宏观裂纹,点焊连接件根部存在微/宏观裂纹。这将损害细胞外壳的完整性。如图11 (b)所示,激光焊接互连线具有较少的微空洞。此外,在某些区域,它没有显示焊接缺陷,这将影响单元外壳的完整性。这证实了Martin J. Brand(2015)的观察。
.jpg)
图10.示出了(a)超声波和(b)激光束焊接的示例,在横截面和浇铸安装之前,以研究焊缝的质量。
图片信用:Buehler
.jpg)
.jpg)
图11.(a)点焊和(b)激光焊接的抛光截面示例。很明显,点焊有更多的空洞,似乎已经穿透更深的外壳材料,并可能破坏电池外壳结构,而激光焊缝是中度穿透。这当然取决于所使用的焊接参数,并且可以优化以最小化观察到的缺陷。
图片信用:Buehler
总结
本文突出了金相准备锂离子电池由圆柱形18650电池类型组成的电池组/模块中的电池。所讨论的方法也可以应用于其他类型的电池,例如那些袋形和棱柱形的设计。还讨论了在切片单元之前需要考虑的安全预防措施,以及与此相关的安装和随后的磨削/抛光过程中的挑战。
此外,还对金相制备的细胞进行了光学表征,并利用电子显微镜对细胞结构的元素组成进行了测绘。此外,还制备了激光、点焊和超声焊缝的细胞互联性,并进行了光学表征。缺陷,包括裂纹和空洞,有关的焊接方法也显示。这是为了突出它们对电池模块/电池组性能行为的影响。
参考文献
- Das, A., Li, D., Williams, D., & Greenwood, D.(2018)。加入技术的汽车电池系统制造。《世界电动汽车》,P22。
- 杜志东(2017)。理解用于高能量密度锂离子电池的厚电极性能的限制因素。应用电化学学报47,405-415。
- 马丁J.品牌,P. A.(2015)。电池电池焊接技术和电接触电阻。储能杂志,7-14。
- 米勒,P。(2015)。乘用车应用的锂离子电池组中的艺术状态和未来发展。约翰逊Matthey技术评论。
- Steen,W. M.(2010)。激光焊接。在激光材料处理中,199-249。
- 萨米特,B。(2018)。材料制备亚博老虎机网登录背后的科学。亚博网站下载Waukegan,伊利诺伊州,U.S.从HTTPS中检索:// www。buehler.com/literature.php.
- Tsiropoulos I., t.n.(2018)。用于移动和固定存储应用的锂离子电池-成本和市场增长的场景。欧盟出版物办公室,2018年。
- 于善善(2013)。高容量锂离子电池lifepo4 /石墨电极设计优化的模型预测和实验。公牛。韩国化学。79年Soc 34岁。
- 周永平(2000)。用交流电源进行小电阻点焊时薄金属片的可焊性。电子材料学报29,1090-1099。亚博网站下载
确认
特别感谢沃里克大学 - IARC
- 能源创新中心团队提供本文中使用的电池罐材,以及用于电子显微镜工作的先进制造和材料中心。亚博网站下载
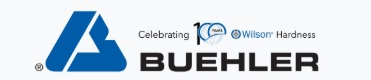
该信息的来源、审查和改编自比勒提供的材料。亚博网站下载
欲了解更多信息,请访问比勒。