真空树脂转移成型,或VARTM,是一种常见和低成本的工艺用于开发风力涡轮机叶片。在这个过程中,由于模内压力和外部大气压的变化,应用真空使树脂流动到单面封闭的模具中的纤维垫预制件中。VARTM是一种高效的工艺,因为它可以生产具有纤维体积分数的复合材料60%以上。因此,该过程可用于制造高质量产品。
Since the molding cycle is longer, slow-reactive and low-viscosity resins are typically selected to guarantee a proper filling without early curing at the time of the filling stage, wherein the resin’s viscosity will be influenced by the shear stress rate, temperature, and curing rate. Moreover, as the curing rate continues to increase with time to the point when the viscosity is sufficiently high for the part to be ejected, the resin can be perceived to be fully cured.
冒险与解决方案面临的挑战
然而,如果在完全固化之前,可能会出现意外出现意外产品变形的问题。为了克服这个问题,工程师应该进行仔细的材料表征测试,以完全了解树脂的固化反应和流变性能,随后使用Moldex3D的非等温,真正的3D仿真技术评估VARTM工艺如何受到各种热固性树脂的影响。下面讨论的是碳纤维风力涡轮机叶片外盖的一个案例。应用Moldex3D的非等温真三维模拟技术,研究不同树脂材料对固化和填充行为的影响。亚博网站下载
首先,通过进行材料表征测试获得树脂A和B的准确流变性和固化行为。然后通过在4小时的时间框架内研究25℃和75℃的树脂A和B的固化和粘度行为的变化。
结果
将材料表征测试的结果与Moldex3D材料向导的结果进行对比,观察到两者呈现出相似的趋势。也就是说,在相同的反应时间下,树脂B的粘度和固化速度都低于树脂A(见图1和图2)。
图1。树脂A和树脂B在25°C和75°C的固化速度。
.jpg)
图2。树脂A和B的粘度在25℃下和75°C。
在这种情况下,使用单面模具的1-kW风力涡轮机叶片作为模型。图3和4分别显示了纤维层和设计布局。固化过程在填充达到99.8%时开始。在此阶段,为了加速固化过程,模具的温度从25℃增加到75℃(图5),允许树脂更快地固化,并且待延迟待喷射的部件。
.jpg)
图3。零件的几何形状和树脂注入设计。
.jpg)
图4。传感器节点在风力涡轮机叶片外盖上的分布。
.jpg)
图5。模具温度设置。
在表1中示出了不同阶段的树脂A和B的粘度,固化速率和固化时间。如图1所示,树脂A具有更长的填充时间和更高的粘度,但具有较短的固化时间。另一方面,树脂B容易填充模具,但具有更长的固化时间。树脂A的总处理时间为2.5小时,树脂B的总处理时间为2小时。
虽然在总的加工时间上只有半小时的差异,但它们的填充和固化时间表明两种树脂之间有很大的差异。简单来说,树脂B比树脂A具有更多的加工优势,因为树脂B的粘度较低,易于填充。因此,可以得出结论,在开始设计之前,应该正确理解材料的特性,以消除不必要的试验和错误。
表1。树脂A和B处于不同阶段的固化速率,粘度和填充时间
|
树脂A. |
树脂B. |
前填 |
固化速度 |
0% |
0% |
粘度 |
710 cps |
154 cps |
填充阶段 |
时间 |
1小时27分钟 |
17分钟 |
固化速度 |
〜11.5% |
0% |
粘度 |
1300 CPS. |
154 cps |
固化阶段 |
时间 |
1小时 |
1小时44分钟 |
固化速度 |
75.00% |
81.40% |
粘度 |
完全治愈 (1.3×109 CPS) |
完全治愈 (2.5×108 cps) |
总加工时间(填充+固化) |
时间 |
2小时27分钟 |
2小时1分钟 |
结论
一般来说,准确控制实际生产设置中的固化时间并不容易。特别是当模具的温度增加时,反应将与材料的材料不同;因此,根据工程师的体验,评估材料属性的变化非常困难。实现更好的控制vartm过程,从Moldex3D的材料向导中获得的材料数据可用于进一步了解各种树脂的材料特性。
此外,通过Moldex3D的充型分析,可以更好地预测树脂的流动行为和固化反应,确定最合适的模具温度和工艺参数,增加使用VARTM工艺的优势。
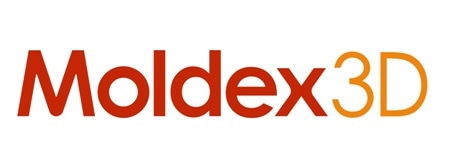
此信息已采购,审查和调整由Moldex3D提供的材料。亚博网站下载
有关此来源的更多信息,请访问Moldex3D。