工程塑料成本低,材料性能优良,越来越多的汽车零部件采用工程塑料制造,如纤维增强塑料阀门。摘要在汽车产品的制造中,纤维增强工程塑料因其高的热变形温度和优异的力学性能而被用于替代金属材料。亚博网站下载
传统的汽车零部件结构分析是基于一种或多种各向同性材料的假设进行CAE分析。亚博网站下载相反,塑料零件的材料性能很大程度上取决于成型工艺。纤维诱导的各向异性力学性能是过程诱导性能,可能不利于最终产品的结构要求。此外,分析结果可能不准确。
的纤维增强热塑性塑料的注射成型这是一个复杂的过程。增强复合材料缺乏各向同性的材料性能,复合材料的力学性能和热性能很大程度上依赖于纤维取向模式。复合材料横向较弱,纤维取向较强。本文通过一个接口程序,将结构分析和注塑成型结合起来,对纤维增强塑料汽车零部件进行结构分析和成型效果分析。
理论
填充
假设聚合物熔体在填充/填充过程中充当广义牛顿流体(GNF)。因此,以下方程式从数学上描述了非等温三维流动运动:
|
(1) |
.jpg) |
(2) |
.jpg) |
(3) |
.jpg) |
(4) |
在哪里
u=速度矢量
T =温度
t=时间
p=压力
σ总应力张量
密度ρ=
粘度η=
k=热导率
CP=比热
ẏ=剪切速率
纤维取向
一个2nd-阶方向向量A表示部分中各点的光纤方向状态:
.jpg) |
(5) |
Advani和Tucker提出了方向张量的方向变化方程,现将其应用于分析:
.jpg) |
(6) |
在哪里C我为相互作用系数,取值范围为10−2到10−3.四阶张量需要闭包近似一个ijkl.
集成方法
该方法将结构分析和充型分析数据连接起来。利用复合材料的力学性能和纤维取向,可以建立纤维增强聚合物的热膨胀系数和各向异性模量。这些各向异性的力学性能将被放入结构单元中进行结构分析。在结构分析中将考虑模具诱导材料的性能。
此外,在结构分析和充型分析中,网格要求可能不一样。结构分析的网格可以集中在应力集中的区域,而充型分析的网格则侧重于比厚度方向更高的单元分辨率。通过该方法,进一步开发了映射函数,将元素属性从模具填充指定的网格映射到结构指定的网格。它准确地匹配元素并映射材质属性,尽管网格属性完全不同,如图1所示。
.jpg)
图1所示。在不同的网格间映射元素属性
结果和讨论
为了验证纤维取向的预测,一个100 x 50 x 1 mm的玻璃纤维增强PET模压矩形板被模拟。填充模式和零件的几何形状如图2所示。浇口位于板的中间。光纤在不同切割平面上的取向如图3所示。
.jpg)
图2。中心浇口板的填充结果
.jpg)
图3。中心浇口板的纤维取向分布
线条的方向表示最有利于方向的方向,每条线条的颜色表示方向的程度。在模壁附近,剪切流可以看到纤维沿着流动排列。在中心切割面上,纤维的流动是无剪切的,因此,纤维的方向与流动方向垂直。预测结果显示了纤维沿焊接线的走向(见图4)。这些分析结果与实验观察结果吻合良好。
.jpg)
图4。侧门板填充结果
图5 (a)为纤维增强工程塑料制成的节流阀。模型采用四节点四面体单元进行网格划分。如图5(b)所示,三个浇口位于同一侧。使用的树脂是PET,它含有50%的玻璃纤维。熔体温度为230℃,模具温度为90℃。填充时间大约为2.0秒。预测的空腔表面熔体锋面分布如图6(a)所示。为了进一步说明这种空洞是如何被填充的,熔体前缘的等值面绘制在图6(b)中。
.jpg)
图5。节流阀型号3闸板
.jpg)
图6。预测熔体前缘分布
所预测的腔体表面和腔体内部的光纤方向如图7所示。这些方向强烈地依赖于填充模式。预测的各向异性力学性能如图8所示。这些属性将被放入后续的结构分析中。整个模压部分的温度被提高到100°C,作为进一步复制纤维增强塑料阀门热变形的外部条件。图9显示了约束条件。这项分析是使用“NENastran”——商业应力进行的。结构分析变形如图10所示,应力分布如图11所示。这些结果表明,应力分布和零件挠度强烈地依赖于注射成型过程。
.jpg)
图7。预测的纤维取向分布
.jpg)
图8。预测的各向异性力学模量
.jpg)
图9。热应力分析的约束集
.jpg)
图10。变形(a)有纤维取向效应的模拟(b)有随机取向效应的模拟。
.jpg)
图11。Von-mises应力(a)有纤维取向效应的模拟(b)有随机取向效应的模拟。
图12(a)和图12(b)也显示了带有两种流道设计的保险杠。该模型为典型薄壁件,平均壁厚2.9 mm。传统的2.5D分析方法易于获得良好的分析结果。7.331采用3节点三角形板单元进行注塑分析。使用的树脂是PET,它含有45%的玻璃纤维。图13(a)和图13(b)显示了两种模具设计的纤维取向分布。不同的模具设计得到不同的纤维取向分布。ABAQUS是一种商用CAE,用于对保险杠进行冲击分析。通过建立由3节点三角形板单元和4节点四边形板单元组成的网格,提高了分析精度,降低了计算负荷,如图14所示。
.jpg)
图12。保险杠模型有两个模具设计
.jpg)
图13。平均纤维取向分布
.jpg)
图14。指定的网格用于冲击分析
利用所提出的映射方法,将纤维诱导的各向异性属性正确地映射到指定的网格上。假设假想车辆在保险杠后的重量为800.0 kgw,碰撞为刚性柱,碰撞速度为4.0 km/h。在图15中,螺栓的固定约束为红点;时间周期为0.5秒。图16显示了任意取向效应的结果,图17和图18显示了各种模具设计的造型诱导取向效应的结果。图19进一步比较了不同模具设计之间传感器节点的位移历史。这些结果表明,注塑件的结构分析与模具设计和成型条件密切相关。
.jpg)
图15.影响分析的模型和约束
.jpg)
图16.随机定向效应的偏转
.jpg)
图17.模具的挠度设计
.jpg)
图18.模具的挠度设计2
.jpg)
.jpg)
图19.传感器节点位移历史(节点1:红线,节点2:浅蓝色线)
结论
在本文中,一个内置的CAE的解决方案对于注塑成型的汽车零件已提出。各种论证的结果表明,纤维增强塑料零件的结构分析很大程度上依赖于成型工艺。该方法可用于零件设计人员对模具设计和零件设计进行评估。这将是塑料零件从设计阶段到制造阶段分析的一个具有成本效益的工具。
参考
[1].S.G.阿德瓦尼,C.L.塔克,J. Rheol。, 31,751(1987)。
[2].“复合材料中的流动诱导对准”,由T.D. Papathansiou和D.C亚博网站下载. Guell主编,剑桥(1997)。
[3].杨文华,徐志伟,杨文尼,张荣勇,“三维短纤维在注塑成型中的计算机模拟,”470,ANTEC 2003, Nashville(2003)。
[4] 彭艾伦、张约克、杨安东尼、杨文妮和庄富强,“注塑节流阀的三维纤维取向和翘曲分析”,第三届汽车复合材料会议,底特律(2003年)。
[5] .CoreTech系统内部报告。
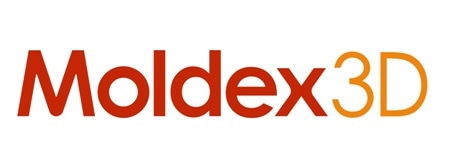
该信息来源于Moldex3D提供的材料,经过审查和改编。亚博网站下载
有关此来源的更多信息,请访问Moldex3D。